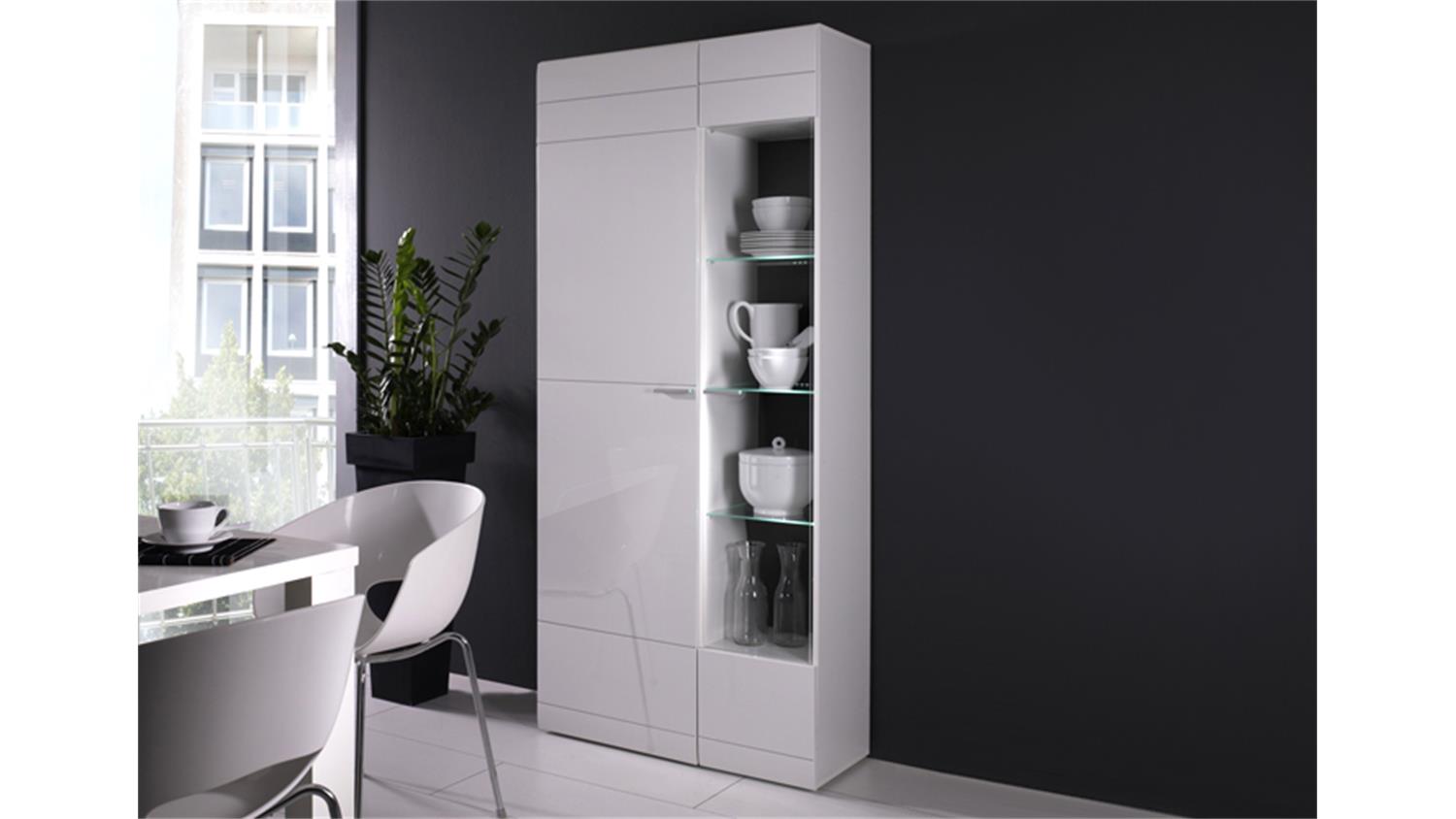
r2-d2 salute you! hello and welcome to quantumstorm's star wars collection. my name is deniz and with this video i would like to open a new category and namely the category "workbench". what will this category be about? it will be about small building projects that have been built around all of the star wars collection. in this special video i will show you for example a showcase which i designed and built. i named this showcase "falt". why "flat"? quite simply because this showcase is only 13 centimeters deep.
what do you need a showcase for?well, i have made this showcase for my still packed figures, so that you can present the figures worthy. foreword several aspects were considered in the construction of my showcase. for example, environmental influences should be kept to a minimum. the objects in the showcases should be protected from uva and uvb radiation, for example. also dust should not "get lost" in these showcases, if possible, because nobody really wants to dust. last, but not least, this should also be a protection against touching if you have viositors.
you know what it's like: the objects are on display, someone comes and touches them, maybe even dumps them. that shouldn't happen and therefore the objects in my showcases are in relatively good hands. besides, i'm not a carpenter, which means that this showcase should be as easy to build as possible. the components for the showcase were cut to size in the diy store. that's because i can't fit a circular saw in my living room and in addition they can produce a relatively high dimensional accuracy in the diy store. this high dimensional accuracy is also important, otherwise some parts in the showcase might not fit together. i also had an aluminium-look edging around some parts,
which fits very well to the other aluminium parts that were used in this showcase. if you want to rebuild this showcase, then the parts list has been listed at the end of the article. these are, of course, the measurements i used. if you want to have other measurements, you would have to change them accordingly. but i thing: talk is cheap - let's get started #1: the showcse base let's get to the showcse base first. the showcse base consists once of the base panel - as you can see here the edging is also on it, in the aluminium look. next there is the floor for the base, or the floor for the actual module. or the floor for the actual module. also here you can see
that this one has been edging with the aluminium-optic. this also includes two side parts. the side parts, we have them here. but they will be attached later. so that the showcse base holds in itself, still have five angles. that these are white doesn't matter, because you won't see the angles later. the angles still need screws, of course. i have normal spax screws here: 4 x 16. 4 x 16 because all the wood has a thickness of 19 mm. a little is still absorbed by the material of the angle. then you only have to look again at the core diameter of this screw. you can use a caliper gauge here...
...i'll take off my glasses for a moment... ... and then we can see that the core diameter here is 2.3 mm. 2.3mm... we would also need such a drill for pre-drilling. so that the wood does not crack. i'll get the drill.see you soon... so, i have once gone into the worm's-eye view... and that's how it's supposed to look in the end. this means that we have our base panel, the bottom of module number one, the lower module. and this aperture should be held with this angle afterwards. i will mark these angles for drill holes with a center punch.
that is relatively exact and so i can apply these angles afterwards. it would be important to mention that we have not yet merged the two parts, that means: first i will only attach the angles to the socket panel, because during the assembly of module #1, resp. of the lower module, it'll be easier if the part isn't on it yet. but we'll see about that later. as you can see, the angles are now in place. why these angles, for the side parts, are not yet in place, we will see later, because this has yet to be drilled. of course, we are not allowed to attach the angles before that.
#2 - scheme of the lower, middle and upper module now comes clearly the more difficult part. cause we're going to have the back plate... ...this part... ...connect it to the base plate. i'll drill 11 holes in the base plate. and then screw these eleven holes later. i'll use these screws for that. of course i will determine the core diameter again, so i can drill the screws right.
the holes are marked and i have already made an exemplary hole here, this is countersunk at the front and has been drilled so big that the screw fits through. here are also the other holes... these are my drilling templates later. this means that the board now comes to the front here, then it is screwed tight in the front and i can use the other holes as a template. pre-drilling is carried out it's being drilled out. it will be lowered
it is screwed together next up is the side panel. i will drill holes here and then take the side parts with as reinforcement. the side piece is what comes to the side afterwards. that means i don't need plexiglass either, because: you can't see through that anyway. [music] the lower body is finished, i.e. the module for the lower body is now finished. you see, this is where i sunk the screws. it's not so bad that they didn't do a good job there.
the main thing is that the screws are really countersunk, because, as i said, you can't see the screws later. that means it's time to put the showcase base on. as you can see, the angles are now also fixed. there's only two pieces left: these are the side walls and i'm going to install them now. it would look like that: one side panel would come here, and the other side panel would come here. i want to fix that again and then we are completely finished with the lower body. except for the details, but they'll come later.
the last pieces of wood are on it. let's see if that thing's standing up. probably not, it still has to be secured against the wall, but we're about to take a look at that. okay, this part is relatively heavy... ...make sure you drop the whole thing... but you can already see how stable the pedestal actually is. now the whole thing comes back to the edge, then we'll look at each other,
... hopla ... if i measured myself. you shouldn't put that on your foot either. then now should fit right in here. it does. the whole thing should look exactly like this and now there are three modules on top. once the center module and the upper module. they're actually made exactly like the module i just did. exception: the middle module gets this plate as the floor,
which means that with a central module only one rear panel and two side panels are required. and the upper module, is actually built exactly like the lower module, with the exception of the base. i am about to drill four holes into the back wall, which will be used for the screws, where the whole module will be fixed to the wall. maybe the best way to do that is to use an angle. i imagined that i would drill here 10 on 10 [cm] because the holes are one, in each case at four corners and which will later act as a drilling template for the wall. it is important here that the module is really aligned in the balance, because on this module all other modules are based afterwards.
as you can see here, the screw holes for the wall mounting are now inside. however, it is so that they are run away, but that does not matter because they are still being lowered. i'm going to call this screwed one we could use a stencil because we might be visible here: the whole thing's not straight. this means that it still has to be aligned first, then the screw holes can be used as a drill template and then the screw holes can be all the screws can be drilled into the wall. i have now brought the whole module once with cardboard so in balance, that the spirit level
now indicates that the system is straight. the holes are in the wall, but watch out: since this is only a 6 hole, but an 8 dowel has to go in, you're gonna have to re-drill it with an 8-bore drill. with a 6er was pre-drilled because the hole in the module is also only 6 mm because the screw has a diameter of 6 mm. as you can see, the screws have now also been inserted and countersunk. the only problem i had was this: a screw will never fit into this hole again because the screw in it has broken off. this happens when you don't drill deep enough and the screw hits the back of the masonry.
the whole thing looks like this. as we can see now, they are all three modules built. that's it, then, as far as the woodwork is concerned. #3: plexiglas carrier now the detailed work has to be completed. in other words, we first need the guide rails for the plexiglas panes. of course the guide rails have to be sawn rightly. a simple metal saw is suitable for this. it is important that the small guide rails come first.
then the plexiglas pane is inserted and only then the long guide rail is inserted, otherwise the small plexiglas pane can no longer be used. the guide rails are applied, as here, on extra strong double-sided adhesive tape, subsequently cut out and then put them where they're supposed to be. the same happens with the longer guide rails, which are then fitted with double-sided adhesive tape and then glued on. that's what it looks like when the first disc is inside. #4: card carrier
the edge for the lower strip is attached to the lower edge with three double-sided pieces of adhesive tape. it is important that the center module is only attached to the rear wall, i.e. not to the rear wall. is glued to the floor. this is because otherwise you cannot disassemble the modules afterwards, because they would stick to each other. and then the whole thing looks like this. also this carrier is fastened again with double-sided adhesive tape, but you have to be careful that you keep the distances for the cards relatively exactly, or the cards will fall over again. on the left side we see that "l" piece which is placed at the bottom.
in the middle we see the unmachined guide rail for the carrier cards. on the right side we can see that the upper bridge has been removed from the guide rail. this is necessary, because otherwise the carrier cards will be connected to the "stem", i.e. the lower plastic part, which is connected to the "bubble," otherwise it wouldn't fit right in there. here you can see how the system should work afterwards. at the top the card is held in the guide rail, and below she stands up on the white splint as normal. now you can insert several cards and create a wall out of figures. as you can see here, the same applies to other toy-lines as well.
this means that as long as the cards are at the same height, the holder on top fits perfectly with the cards. ready! this is what the end result looks like. i love it when a plan works! in the lower area you can see that this toy-line does not fit to the standard dimensions, therefore the dimensions for the guide rail were adapted here. rã©sumã© in conclusion, it can be said that the construction of the showcase was relatively successful. the only thing i might change in a later replica is the structure of the carrier card holders. now i had to carve them with a cutter, that was first of all a rather fiddly work and
secondly, it has taken a relatively long time. but basically: the result speaks for itself. the objects are now protected and are also beautifully displayed. so: i am satisfied! parts list and tool used i hope you enjoyed my homemade project. if you have any questions or comments, please write them to me below and if you like you can also subscribe to the channel right away then you won't miss any future videos. in that sense, i'd say:bye and until then from the
quantumstorm's star wars collection